High-Speed Die-Cutting Using compound dies
Covering the whole range of washers for bolted assemblies, our compound die-cutting tools produce washers that are perfectly flat and perfectly concentric at very high throughput.
- Fully automated 200-tonne lines
- Thickness: 0.5 to 7 mm
- Manual stamping presses from 160 to 250 tonnes
- Maximum thickness: 10 mm
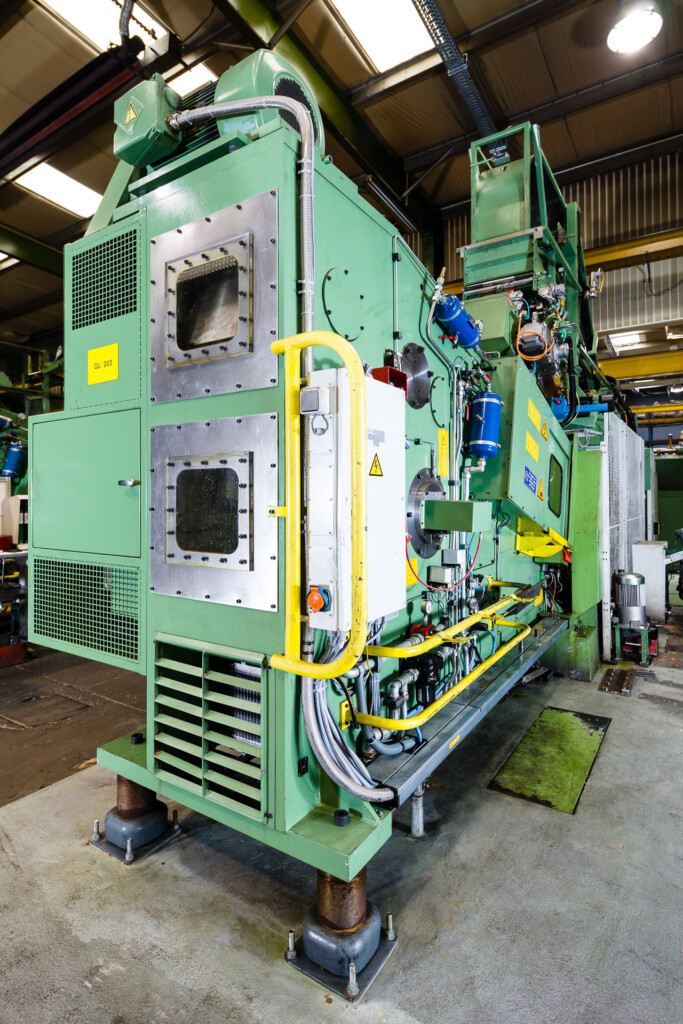